It is a time-consuming skilled trade and Petter exercises great care in every aspect of his work. He draws his hand over the recently effected woodwork repair and decides that it is now perfect.
Tell us a little about your background, because you have not always worked with joinery?
What I have done the most to date is working as a contemporary circus artist. That involved acrobatics, juggling and fire artistry in various forms. I have always been attracted to doing difficult things and enjoy practicing things that are difficult, or preferably totally impossible.
How is it that you finally ended up doing joinery?
I’ve had woodworking in my blood since childhood. After high school I took courses in restoration architecture at the Faculty of Engineering at Lund University to qualify as a restoration architect. But it turned out to be far too administrative and hierarchical for me. I did not fit in there at all; I wanted to work with my hands as well.
I gave up that idea and continued working with my artistry. It was only when I met an old window craftsman that I realized what I wanted to do. After 12 years as a professional contemporary circus artist I started my own window joinery company in 2014.

"Changing windows because they are drafty, is like scrapping your car because the tires are getting worn."
How many window joiners are there in Sweden?
It’s hard to say, as many avoid the limelight. Most of them are very busy and don’t need to market themselves. I am one of them, and maybe there are 200 of us in total. I know of around 100 joiners.
It doesn’t sound like you have to hunt for customers?
Oh no, customers come chasing me. (Laughter) However, I thought it was hard to find good information when I started as a window joiner, so that’s why I’m sharing my tips on social media. In turn it has given me work and created attention. It’s my best marketing effort - to share what I do.
"I have lots of power tools that help me work efficiently, but they make noise and create dust, and often cause me to take me a step further back from the workpiece."
What is the best thing about your job?
A job that ticks all the boxes would involve worn-out antique windows that belong to a customer who has been searching for someone to restore them for long time. The most beautiful parts are cutting the glass, applying the putty, removing damaged timber and achieving a perfect fit in the replacement pieces. To plane away the last tenth of a millimeter and witness the old and the new fuse together.
At the same time the work is very varied - sometimes I get to hew in concrete, only in the next moment to cut 200 year-old hand-blown glass, or hang a frame 15 meters up in the air.
"To plane away the last tenth of a millimeter and witness the old and the new fuse together."
I understand you mainly use hand tools?
The right tool for the right task I would say. Many times, it is easier and faster to work by hand than to pick up machines and configure them for the job. I have many power tools that help me work efficiently, but they make noise and create dust, and take me further away from the craft.
What tools could you not manage without?
I couldn’t do without a lot of tools! But what I would miss the most would be the HDC Chisel that I always have on my belt. And the Japanese saw that I wouldn’t want to be without. The HDC Chisel’s planing function makes it possible to get to where other chisels cannot reach, and the iron sole gives me immediate feedback on the smoothness of the surface I managed to accomplish.
What does a typical work day look like for you?
There are probably ten different typical days. Work inside the workshop may involve taking inventory, measuring, removing glaze and scraping paint, or inserting timber restorations, maybe cutting glass, applying putty and paint or linseed oil-burning old iron fittings.
A customer might have a dormer window that’s leaked water and needs to be refurbished, or I’ll be standing on a scaffold sawing off bad timber on a frame. I must have duplicates of all the important tools as I can never really know what I might find under metal and paint.
"I’ve always been attracted by doing difficult things."
Have you ever refused a job that you considered to be impossible?
I have refused jobs, but not because they have been impossible. It was more a case of them sometimes becoming too expensive. For example, I’ve had jobs consisting of 1980s windows set in substandard timber with bad glass. That type of project costs a lot more than it is worth. But there are really old windows jobs that even if only 10% of the window sash remains and the rest is new, I’ll do them if it’s economically viable.
What is important to consider in a restoration project?
The most important thing is that linseed oil products are used, something that has worked for several hundred years and is the only thing that nurtures the old material properly. Getting wood repairs to fit perfectly is also crucial for them to be able to last for quite some time.
Do you have any tips & tricks, or do you keep them to yourself?
I am very happy to share them. What I do is hard enough, so I don’t have to hold on to any trade secrets. I use the chisels for most projects, and I need to resharpen the blade often. But I can’t stand water grinding, it takes far too long. Instead, I use a belt sander because it doesn’t burn the edge as much as a whetstone does.
Before grinding, I throw the chisel into the freezer. The HDC Chisels are made from sufficiently heavy density iron so they remain chilled much longer, which means that I can belt-sharpen a new edge without worrying about it burning. Then I sharpen the raw edge and fine-polish it using a bench-polishing machine with polishing paste. It takes no time at all to get a nice, sharp edge. It is of course not as perfect as with a Japanese whetstone, but it is quite sufficient for most of the work that I do.
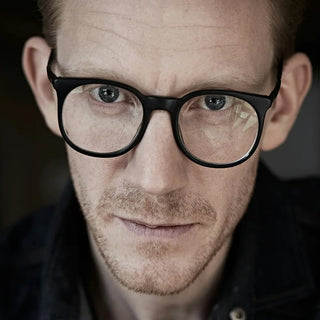
Facts